Properties and Applications of Soft Magnetic Materials
Materials which have a steeply rising magnetization curve, relatively small and narrow hysteresis loop and consequently small energy losses for each cycle of magnetization are called soft magnetic materials.
Soft magnetic materials are, therefore, employed in building cores for use in alternating magnetic fields. The commonest soft magnetic materials are soft iron, nickel-iron alloys, and soft ferrites.
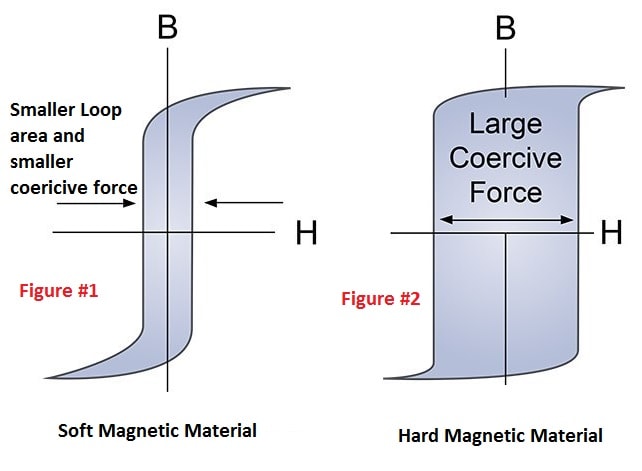
Soft magnetic materials are used for the construction of cores for electric machines, transformers, electromagnets, reactors, relays, etc. The economic construction of such equipment demands that the magnetic flux should be produced in the minimum space and with minimum loss.
Requirements of Magnetic Materials
We already know that : flux = flux density x cross-sectional area, i.e. φ = B x A.
To obtain a given value of the flux, we must choose a high value of flux density. In order to keep the minimum, the cross-sectional area means less quantity of material. However, a large flux density means correspondingly large eddy current and hysteresis losses.
Furthermore, a value of flux density above saturation value should not be chosen as this will give rise to a large magnetizing current. Saturation value is that value of flux density (B) at which the B-H curve starts bending and tends to become horizontal.
Using a low flux density in order to keep the magnetizing current and the iron losses low will call for an increase in cross-sectional area of the magnetic path which means more iron.
In view of the above discussion, a compromise is made in actual practice while choosing the flux density for a given application so that the amount of the magnetic material used (i.e. the capital cost) and the iron losses (i.e. the operating cost) are kept as low as possible.
The magnetic material for the core of electrical machines and transformers should have high saturation value and permeability to keep the magnetizing current within reasonable low limits. When the core is to be used for alternating magnetic fields the core should be of such a material as to produce small iron losses (hysteresis and eddy current losses).
To sum up, the requirements of magnetic materials for use in electrical machines and transformers are :
- A small enclosed area of hysteresis loop;
- High permeability;
- High saturation value of flux density.
The core of electrical machines and transformers must be made of laminations for reduced eddy current losses.
Properties and Applications of Pure Iron
By the term pure iron is meant a ferrous material with extra-low carbon content. The examples are low-carbon steel and electrolytic iron. In low-carbon steel carbon content is less than 0.1 percent. By appropriate manufacturing techniques, high magnetic permeability and low coercive force can be obtained.
However, the resistivity of pure iron is very low by which it gives rise to large eddy current losses when operated at high flux densities in alternating magnetic fields. This limits their use to fields carrying steady flux (dc field) or weak alternating, current fields.
Technically pure iron is widely used in many kinds of electrical apparatus and instruments as a magnetic material core for electromagnets, components for relay electrical instruments, etc. Pure iron is not used in rotating electrical machines where rotation of the slotted rotor causes variation reluctance and, therefore, of flux.
Properties and Applications of Iron-Silicon Alloys
Application of pure iron is limited because of its high eddy current losses. By incorporating small quantities of other elements in iron good magnetic properties are obtained. The chief alloying constituent is silicon which is added to iron in amounts from 0.5 to 5% by weight. Such alloys are generally known as silicon steel.
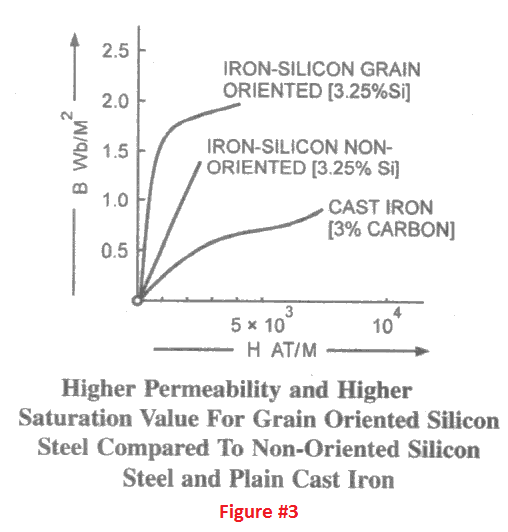
Silicon sharply increases the electrical resistivity of iron thus decreasing the iron losses due to eddy currents. It increases the permeability at low and moderate flux densities but decreases it at high flux densities. Addition of silicon to iron reduces hysteresis loss. The magnetostriction effect is also reduced.
Besides improving the magnetic properties of iron, the addition of silicon is also valuable because it facilitates the steel making process. Alloying of low-carbon steel with Silicon increases the tensile strength; however, it reduces ductility making steel brittle. This makes silicon alloyed steel difficult to punch and shear. A steel with more than 5% silicon may be too hard and brittle to be easily workable.
This means that high silicon steel has high permeability but comparatively lower saturation. High silicon sheet steel with a silicon content of about 4% is used chiefly in the magnetic circuits of power transformers which operate at flux densities of about 1 Wb/m2.
However, since the cores of rotating electrical machines are slotted with the teeth having a small cross-sectional area, the flux density in the teeth is much higher, of the order of say 1 Wb/m2. To obtain high flux density in the case of high silicon steel, the magnetizing current necessary is very large. Also punching slots in high silicon steel would be difficult because it is harder and more brittle. For these reasons low silicon steel with a silicon content of about 2% having a higher saturation value is used in the cores of electrical rotating machines.
A comparative study of the magnetization curves of high silicon and low silicon steels is given in Fig. 5.30. The most common thickness of electrical sheet steel (i.e. sheet steel used in making cores for electrical equipment) ranges between 0.35 mm and 0.5 mm. Thinner laminations, as small as 0.1 mm, are used in high-frequency equipment.
Properties and Applications of Nickel-iron Alloys
Permeability of iron and iron-silicon alloys in weak magnetic fields is relatively low. For power applications like transformers and rotating electrical machines, where core materials are operated at high flux densities, the initial permeability is of no importance.
But for high sensitivity and low distortion required in communication systems, the iron-silicon alloys are not suitable. Special magnetic alloys having initial and maximum permeability are used for special applications like instrument transformers, relays, etc.
A group of iron alloys containing nickel between 30 to 80 percent with the possible addition of molybdenum and chromium when given appropriate treatment during manufacture, show very high permeabilities at low flux densities and much lower losses than iron. The important alloys in this category are Permalloy, Supermalloy and Mumetal.
Permalloy: This is used in the manufacture of sensitive relays. The curie temperature of this group of the material varies between 420 to 580°C depending on the percentage of nickel content and heat-treated up to about 1,050 to 1,100°C. It has initial permeability varying between 2,500 to 8,000 whereas maximum permeability reaches as high as 1,00,000.
Superalloy: It consists of iron and nickel alloyed with copper and molybdenum. This alloy is distinguished by its high initial permeability up to 1,00,000.
Mumetal: It consists of iron and nickel alloyed with copper and chromium. It is used for manufacturing instrument transformers and miniature transformers (used in communication circuitry). It is heat-treated up to 100°C and having a curie temperature of 430°C. Its initial permeability is 20,000 and maximum is 1,10,000.
Properties and Applications of Soft Ferrites
Ceramic magnets, also called ferromagnetic ceramics and ferrites, are made of iron oxide, Fe203, with one or more divalent oxides such as NiO, MnO or ZnO. These magnets have a square hysteresis loop and high resistance to demagnetization and are valued for magnets for computing machines where a high resonance is desired.
The great advantage of ferrites is their high resistivity. Commercial ferrites can have resistivities as high as 109 ohm-cm. Eddy currents resulting from alternating fields are, therefore, reduced to a minimum, and the range of application of these magnetic materials is extended to high frequencies, even to microwaves.
Ferrites are carefully made by mixing powdered oxides, compacting and sintering at high temperatures. High-frequency transformers in television and frequency modulated receivers are almost always made with ferrite cores. Ferrites, with large magnetostrictive effects, are sometimes used in electromechanical transducers. In high-frequency application, magnetostriction in ferrites can lead to undesirable noise.
Materials which have a gradually rising magnetization curve, large hysteresis loop area and consequently large energy losses for each cycle of magnetization are called hard magnetic materials.
Hard magnetic materials are used for making permanent magnets. The desired properties of material required of making permanent magnets are high saturation values, high coercive force, and high residual magnetism.
It is seen from Figure #2 that the product of B and H for a hard magnetic material is high compared to that for the soft magnetic material. In a hard magnetic material, it is difficult to orient the domains as compared to the soft magnetic materials. Thus it is difficult to magnetize a hard magnetic material. The coercive force is large and hence the material is magnetically hard. In a very hard material, the domain walls may be absolutely immobile.
Properties and Applications of Carbon, Tungsten, Cobalt Steel
Soft magnetic materials cannot be used for making permanent magnets because they have narrow hysteresis loops. It has been seen that when carbon is added in material, its hysteresis loop area is increased. That’s why in early days carbon steel was used for permanent magnets. Although it is cheap, magnets made from carbon steel lose their magnetic properties very fast under the influence of knocks and vibrations.
When materials like tungsten, chromium or cobalt are added to carbon steel, its magnetic properties are improved. Cobalt steel has exceptionally superior magnetic properties but is expensive.
Properties and Applications of ALNICO
Alloys like ALNICO (Aluminium-nickel-iron cobalt) are commercially the most important of the hard magnetic materials. Large magnets are made by special casting techniques and small ones by powder metallurgy. As compared to cobalt steel it is cheaper.
Alnico is an exceptionally hard magnetic material and due to this reason nowadays permanent magnets are most commonly made of Alnico. High-quality permanent magnets are used in many electrical engineering applications e.g. in various electrical measuring instruments.
Properties and Applications of Hard Ferrites
These are ceramic permanent magnetic materials. The most important family of hard ferrites has the basic composition MOFe2O3, where M is a barium (Ba) ion or a strontium (Sr) ion. These materials have a hexagonal structure and low in cost and density. Hard ferrites are used in generators, relays, and motors. Electronic applications include magnets for loudspeakers, telephone ringers, and receivers. They are also used in holding devices for door closers, seals, latches and in several toy designs.
There is another category of magnetic materials, known as super-paramagnetic, made from powdered iron or other magnetic particles. These materials are used in transformers for electronics and cores for inductors. Permalloy (molybdenum-nickel-iron powder) is the best-known example of this important category of magnetic materials.
Thanks for reading about “applications of soft and hard magnetic materials”.
Related Posts
- Dia Para Ferro Magnetic Materials
- Applications of Soft and Hard Magnetic Materials
- Why CRGO core is used in transformers?
- Properties of High Resistivity Materials
- Properties of Insulating Materials
- Applications of Insulating Materials
- Properties of Superconductors
- Dielectric Strength | Constant | Loss | Definition
- Creep in Materials
© www.yourelectricalguide.com/ application of hard magnetic materials.